Packaging Machine Repair Service: Prevent Pricey Malfunctions with Professional Aid
Packaging Machine Repair Service: Prevent Pricey Malfunctions with Professional Aid
Blog Article
Recognizing the Key Parts and Repair Service Methods for Product Packaging Maker Maintenance
Reliable upkeep of packaging devices depends upon a comprehensive understanding of their vital parts, including the framework, drive system, and securing systems. Acknowledging usual maintenance concerns, combined with the application of preventative approaches and repairing strategies, can significantly improve maker dependability. The selection of fixing methods, including the usage of OEM components and the value of qualified service technicians, plays a critical function in decreasing downtime. To really grasp the details of these systems and their upkeep, one must consider the wider implications of overlooking these essential techniques.
Secret Components of Packaging Devices
Product packaging devices include numerous essential elements that interact to make sure reliable and effective product packaging procedures. At the core of these machines is the structure, which gives structural stability and houses the various operating parts. The drive system, often a mix of equipments and motors, promotes the movement of elements, enabling precise procedure throughout the product packaging cycle.
Another important element is the conveyor system, which delivers products through different stages of the product packaging procedure. This is frequently matched by sensing units and controls that keep an eye on the placement and speed of items, ensuring synchronization and reducing mistakes. The loading system is vital for accurately giving the appropriate quantity of product right into packages, whether in liquid, powder, or solid form.
Sealing systems, consisting of warm sealers or sticky applicators, play an essential duty in safeguarding bundles, preventing contamination and prolonging service life. Additionally, classifying systems are indispensable for offering essential item info, making certain conformity with regulations. The control panel, geared up with easy to use user interfaces, enables operators to handle maker features, screen efficiency, and make changes as needed, ensuring optimum productivity and efficiency in product packaging procedures.
Typical Upkeep Concerns
Effective operation of packaging equipments counts heavily on regular upkeep to protect against typical issues that can interfere with manufacturing. Among these issues, mechanical deterioration prevails, particularly in components like seals, electric motors, and conveyors, which can bring about unexpected downtimes. In addition, misalignment of components can lead to inefficient operation, causing products to be inaccurately packaged or damaged during the procedure.
An additional usual upkeep issue involves the accumulation of dust and debris, which can hinder the machine's sensors and moving components. packaging machine repair service. This not only influences performance however can likewise present safety dangers. Moreover, lubrication failures can lead to raised rubbing, causing overheating and eventual part failure.
Electrical problems, commonly originating from loose links or worn-out circuitry, can interrupt machinery functions, resulting in significant production hold-ups. Last but not least, software application glitches because of obsolete programs or incorrect configurations can prevent the equipment's operation, requiring instant treatment. Attending to these usual upkeep issues proactively is vital for ensuring optimal efficiency and durability of product packaging equipment.
Preventative Maintenance Approaches
Executing preventative maintenance techniques is critical for sustaining the effectiveness and integrity of packaging equipments. These techniques encompass an organized method to upkeep, concentrating on the routine examination and maintenance of equipment to preempt potential failures. By adhering to an arranged maintenance program, operators can recognize wear and tear on parts prior to they cause substantial malfunctions.
Crucial element of a preventative upkeep strategy consist of routine inspections, lubrication, component, and cleaning replacements based on manufacturer visit our website referrals. Making use of checklists can streamline this procedure, guaranteeing that no crucial jobs are ignored. In addition, maintaining accurate records of upkeep activities help in tracking the machine's efficiency over time, assisting in informed decision-making concerning future upkeep requirements.
Educating staff on the value of preventative upkeep boosts compliance and fosters a culture of aggressive care. Carrying out a predictive upkeep element, utilizing information analytics and sensing unit modern technology, can better optimize equipment efficiency by anticipating failures before they take place.
Troubleshooting Techniques
When encountered with breakdowns or inefficiencies in product packaging machines, utilizing organized troubleshooting strategies is necessary for identifying and dealing with problems quickly. The initial step in efficient troubleshooting is to develop a clear understanding of the equipment's functional specifications and efficiency metrics. This includes examining the device's specifications, as well as any type of mistake codes or signals presented.
Following, drivers must perform a visual examination, looking for apparent indications of imbalance, wear, or damage. This usually consists of analyzing sensors, gears, and belts to determine prospective reasons for breakdown. Collecting operational information, such as production rates and downtime logs, can additionally provide insights into repeating problems.
Once prospective issues are determined, using a rational strategy to separate the source is important. This may need testing individual parts or systems in a regulated manner. Engaging in conversations with operators that communicate with the equipment routinely can generate beneficial comments about unusual actions or patterns.
Fixing and Replacement Best Practices
An extensive understanding of repair work and replacement ideal methods is vital for preserving the longevity and efficiency of packaging Read Full Report machines. Frequently analyzing the problem of device components enables timely treatment, avoiding even more substantial problems that can lead to expensive downtimes.
When repair services are necessary, it is vital to use OEM (Original Devices Supplier) parts to make sure compatibility and efficiency. This not only preserves the stability of the device yet also maintains guarantee arrangements. Furthermore, it is suggested to keep an inventory of crucial extra parts to facilitate quick replacements and lessen operational disturbances.
For intricate repair work, involving certified service technicians with specialized training in product packaging machinery is advised. They have the proficiency to diagnose issues properly and carry out repairs successfully. Moreover, recording all repair service activities and components substitutes is vital for preserving a detailed upkeep background, which can aid in future troubleshooting.
Last but not least, applying an aggressive strategy, consisting of regular examinations and predictive upkeep techniques, boosts the reliability of packaging makers. By adhering to these best practices, businesses can make sure optimal device performance, lower functional dangers, and expand tools life-span.
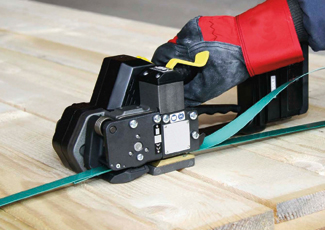
Verdict
In verdict, an extensive understanding of product packaging device components and effective upkeep strategies is essential for optimal performance. Regular examinations and making use of OEM components can dramatically minimize downtime, while a well-documented upkeep history cultivates proactive care. Employing certified service technicians even more boosts repair work quality and reliability. By carrying out these methods, organizations can make certain the long life and efficiency of packaging devices, ultimately adding to improved functional efficiency and decreased prices.
Reliable maintenance of useful reference product packaging devices hinges on a detailed understanding of their key parts, including the framework, drive system, and securing mechanisms.Efficient procedure of product packaging devices depends heavily on normal maintenance to avoid typical issues that can interrupt manufacturing.Implementing preventative maintenance approaches is essential for sustaining the performance and dependability of product packaging equipments. Furthermore, keeping precise records of maintenance activities aids in tracking the maker's performance over time, helping with educated decision-making pertaining to future maintenance requirements.
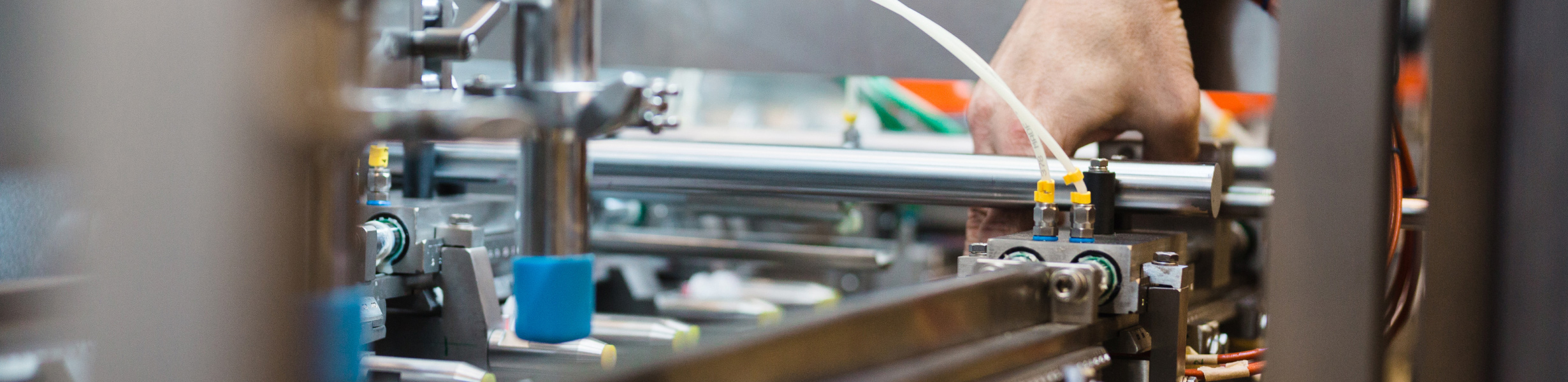
Report this page